Defence manufacturer
This manufacturer supplies high-tech defense equipment to a number of major countries.
After completion, a multi-year maintenance and replacement service is also provided to its customers.
For its customers, it is crucial that the parts are returned quickly and correctly worldwide with a logging of the changes.
This process involves many steps with multiple stakeholders (such as carriers, customs, suppliers and the customer).
This service was supported by an outdated access tool and included many manual and paper-based steps with few explanations. In between, a lot of data was also exchanged manually with the BAAN ERP package.
No uniform working method
- The department was at a loss for words about ordered parts and who had what action to take;
- Employees had their own ways of working, so there was no clear workflow and the acceptance of a new uniform solution seemed challenging.
No tracking
Due to the many manual actions and physical documents that were exchanged, there was a poor overview of where parts were located and the status of ordered parts.
Distributed data
The data to arrive at an insight was scattered in various systems that were not linked and were also largely hidden in mail exchanges.
Not a good product catalog
- The parts that make up the end products have their own life cycles;
- Before ordering and replacing parts, it is therefore important to have insight into which parts are end-of-support AND which new parts can be used as replacements.
Shipping inefficiency
Arranging a shipment meant that many packing slips were created in Word files and then had to be manually entered into other systems. Then following the shipment status meant calling again or logging into external portals per shipment.
Uniform working method
In extensive workshops, Quatronic has coordinated one widely supported way of working/workflow with the customer. This is crucial as the basis of a successful project because the end users must embrace it.
Maintenance and replacement portal
To support the process, a portal was delivered with:
- A workflow for each request with many automatic checks, communication and data consultations from other sources;
- A dashboard to immediately see what the most important tasks are to tackle (even when tasks are invested externally);
- A product catalog to immediately recognize which parts need to be ordered and from which suppliers this is possible;
- Automated packing slip generation;
- Automated order generation for shipments to third parties and retrieving updates about shipments;
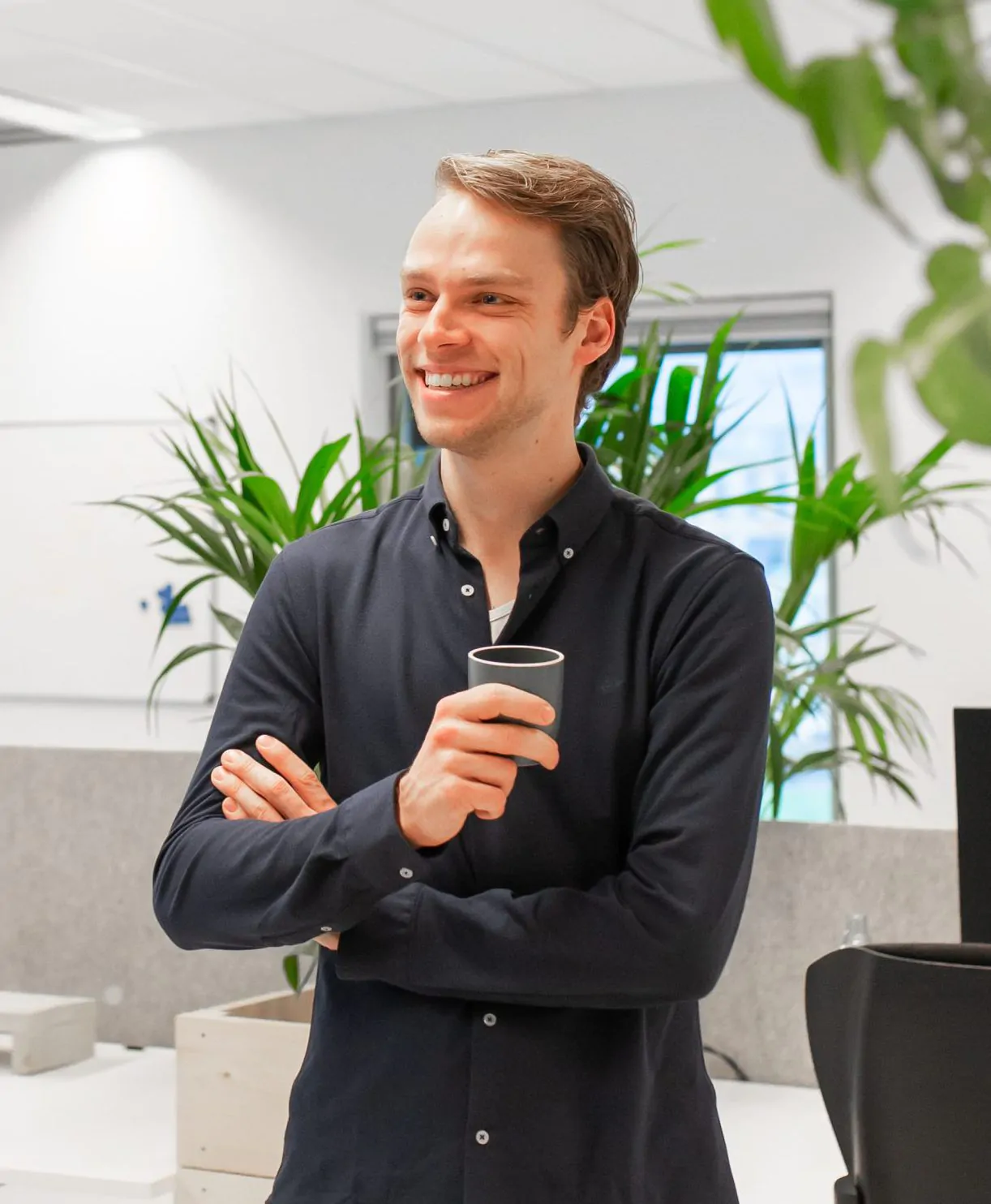