Learn why it's important to improve your processes before digitizing and learn how to digitize optimally.
Technology is changing at a rapid pace and the world is changing with it. Many companies are feeling the pressure to digitize, driven by the benefits of efficiency, better customer interaction and data-driven decision making. But beware: thoughtless digitization can actually cause problems. It is important to first properly map out and improve your existing processes before you start digitization. After all, digitization is not an end in itself, but a means of working more efficiently. In this blog, Maud van Paassen, Business Technology Consultant at Quatronic, explains how to successfully optimize and digitize your processes.
Start improving your processes
There is already a lot of profit to be made by improving your business processes. Workflows develop over a long period of time and are not always viewed critically. They are often caused by limitations in systems or because there is simply no system. Each department then creates its own solutions, which are then linked together. When you ask why something happens in a certain way, the answer is often: “That's just how we do it.” It is precisely by taking a good look at that way of working that you can already take big steps. If you digitize without addressing those inefficiencies, your solution probably won't add the value you expect. After all, the processes are still not properly aligned with reality.
Digitization is not a goal, but a means of process improvement
Digitization should never be a goal in itself. It is a means of improving processes. This is in line with the LEAN philosophy, which emphasises the importance of eliminating inefficiencies and improving working methods. An example of this is the “countermeasure ladder”, an effective tool from the TPM methodology, which helps to address the root causes of problems. Although this model was originally developed for the manufacturing sector, the principles can also be applied more widely.
The first step in this process is awareness of the optimal way of working and training employees in this regard. The second step is to validate whether employees have correctly understood and remembered this method. This can be done, for example, by means of an audit or other evaluation methods to check whether the processes are properly followed and continue to provide added value. Then, together with the team, you can see how work procedures can be further standardized, for example by using visual aids to ensure consistency and quickly identify problems. In a next step, known as Poka Yoke, you build in smart controls to prevent errors. Automation is often a logical step after process optimization, but it does not have to be long in coming. This can even be carried out in parallel with the improvement of work procedures. Through this step-by-step approach, you create a solid basis, so that digitization can be implemented more sustainably and efficiently.
Three reasons not to automate too quickly
1. Understanding your process: If you automate without knowing the process, you may be digitizing inefficiencies and bottlenecks. This can aggravate existing problems rather than solve them. It's important to first identify the bottlenecks and understand which steps are really necessary.
2. Cost savings: Automation is expensive. By optimizing your processes first, you make the technology less complex, making maintenance easier and cheaper. This way, you can make optimal use of the benefits of digitization.
3. Employee engagement: When employees are actively involved in process improvement, they accept new tools more quickly. This creates a culture of continuous improvement and innovation, in which the adoption of new technologies runs smoothly.
IT as a strategic asset
Once your processes are in order, it forms the basis for effectively using IT as a strategic differentiator. After all, digitization goes beyond just automation; it offers the opportunity to innovate and improve processes. Once upon a time, IT was mainly supportive and you had to adapt your way of working to the systems. Thanks to low-code, you can now use customized solutions to optimize and reshape processes. As Rob said in an earlier blog, customization is really not necessary for HR or CRM procedures, your accounting or office applications. An off-the-shelf solution is fine there. But for your core processes, where your distinctive character lies, you make the difference with customization.
How can Quatronic help?
We understand that digitization is far-reaching and sometimes difficult to oversee. That's why we help companies map out their processes and make improvements, even before digitization. Together, we ensure that you are not only ready for digitization, but that you also get the most out of your investments. When organizations come to us, they often already have a plan ready. That's good, of course, because doing research beforehand is important. Nevertheless, we always take the time to go back to the drawing board. We want challenge your plans and optimize where necessary. At Quatronic, we build what you need, not just what you ask for.
The practice: Cheesepop food group
Bee Cheese-pop we have applied this structured approach. The organization was facing major changes: a new factory and an expansion from B2C-only to a combination with B2B. This resulted in new products and working methods. After researching standard solutions, Cheesepop consciously opted for customization with OutSystems. They wanted to innovate instead of adapting their processes to a standard solution. Before we started digitizing, we identified and improved the working methods together with the team. This resulted in more efficient processes, less rework and a higher adoption of the system. Even the biggest digitists eventually fully embraced the new system.
Curious?
Are you ready to optimize your processes with OutSystems? Take contact set out to explore the possibilities and take the step towards a more efficient, agile future today.
Want to stay up to date?
Is now not the time, but are you curious about our blogs and articles? Then follow our LinkedIn page and you'll be the first to know about our latest contributions and future events.
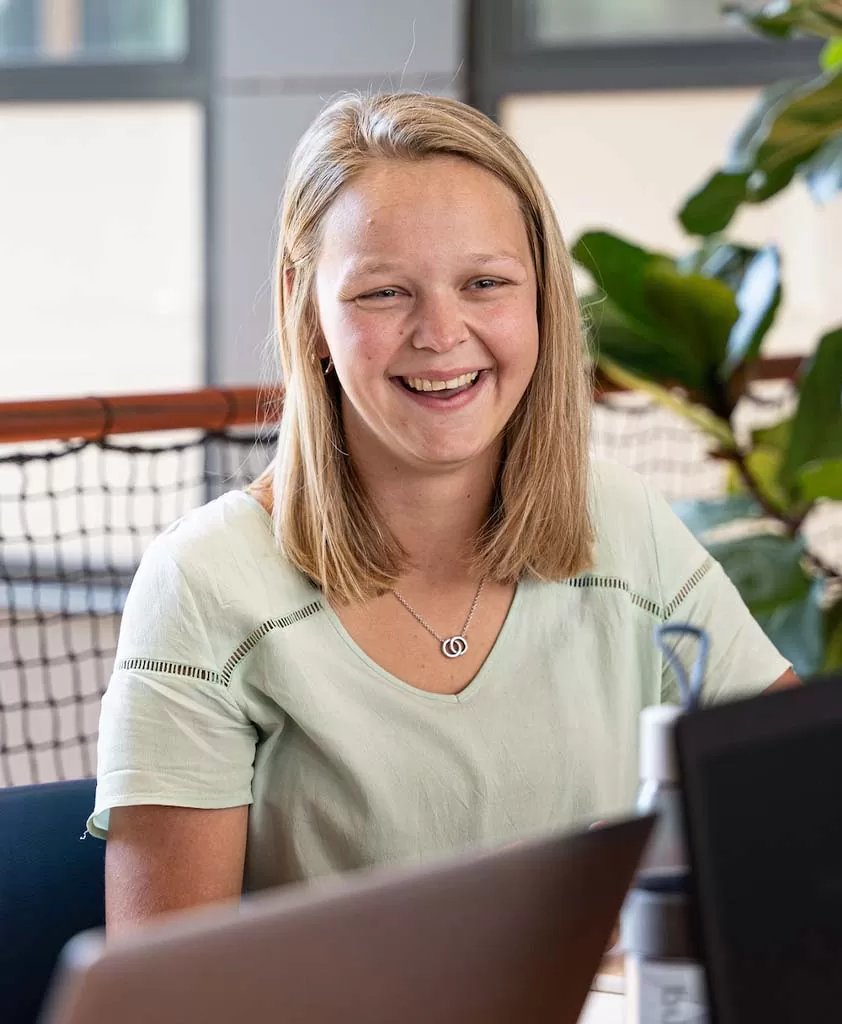