When organizations opt for customized solutions, they naturally expect them to perfectly suit their needs. At Quatronic, we think that's only logical. But how do we manage to deliver that perfectly appropriate customization in a consistent way? As crazy as it sounds: with a standardized approach. In this blog, Wouter van der Meij, Co-Founder of Quatronic, takes you through the three phases of our standardized approach: Discover, Develop and Drive. Discover how we always achieve results with this approach that make both us and our customers happy.
Discover: Understanding the Problem
At Quatronic, we start by thoroughly understanding the problem. We organize workshops where we meet with all stakeholders to gain an interactive insight into your business processes and challenges. Even if you already know what you want — or better yet, think you know what you want, we organize this creative workshop. As you can see, a little bit of stubbornness is no stranger to us. This way, we not only sharpen your needs, it also creates a shared understanding. We end with a prototype, a visual representation of how the software could work. The design workshop is the starting point for our further process.
Develop: Iterative development with full transparency
After the Discover phase, we translate all insights and ideas into workable requirements, which we get to work on. We use OutSystems' low-code platform, which allows us to work in visual environments and develop iteratively in sprints, usually two weeks. After each sprint, we deliver new software and show you the progress. This ensures full transparency and allows us to continuously collect and adjust input. The result is an efficient development process, while maintaining quality.
Drive: Implementation, Training, and Optimization
In the Drive phase, we will implement and take control. We train your employees, observe how the software works in practice and adapt where necessary. We measure performance and evaluate whether the solution actually meets the set goals. The most important thing is that we remain flexible in this phase, sit on top of the process and switch quickly by making adjustments when necessary. No matter how brilliant an idea is, in practice, it can always prove less effective than expected, and then we adapt it. Through this iterative approach, we ensure a successful implementation. After going live, the process doesn't always stop. Develop and Drive are not separate. It often happens that we still develop plenty of new functionalities while the solution is already live.
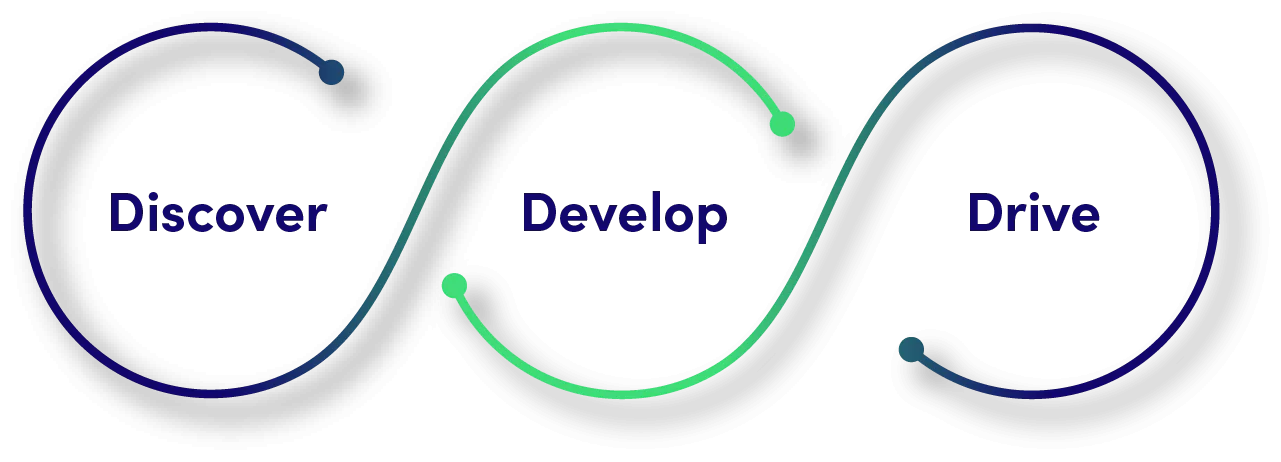
Benefits of our standardized approach
Our standardized approach offers significant advantages. First, we work with the same Quatronic team throughout the process. As a result, there is no noise: the person who understands the business and attends the design workshop also builds the solution. In addition, our standardized approach ensures speed and quality. Take a car brand like Toyota — a company I worked with while I graduated in Japan. Every Toyota comes off the same assembly line and yet every car is customized. The manufacturing method has been standardized, but the result is always different. In fact, that's how it works for us too. By consistently applying the same method, we can guarantee speed and quality.
Continuous learning and improvement
As with Toyota, the concept of Poka Yoke — Japanese for error prevention — part of our “production process”. Making mistakes is human, but you have to learn from them. The SIM card is a great example, there is only one way you can put it in the phone because a corner is out. Of course, that once went wrong, when someone thought: how can we prevent people from putting that SIM card in their phones incorrectly over and over again? This way of thinking is also deeply rooted in our corporate culture and allows us to continuously improve and thus create maximum value over and over again.
Curious about our approach?
Do you also want to benefit from Quatronic's standardized approach and customized solutions? Please contact Wouter van der Meij via mail or give him a call on 06 1340 7347 and we'd love to talk to you to find out how we can help improve your business.
Want to stay up to date?
Is now not the time, but are you curious about our blogs and articles? Then follow our LinkedIn-page and you'll be the first to know about our latest contributions and future events.